*This position will regularly report to Laconia, New Hampshire, United States*
Careers that Change Lives
A career at Medtronic is like no other. We’re purposeful. We’re committed. And we’re driven by our Mission to alleviate pain, restore health and extend life for millions of people worldwide.
Join a diverse team of innovators who bring their worldview, their unique backgrounds and their individual life experiences to work every day. It’s no accident – we work hard to cultivate a workforce that reflects our patients and partners. We believe it’s the only way to drive healthcare forward and remain a global leader in medical technology and solutions.
In this exciting role as Principal Manufacturing Engineer, you will be driving the resolution of issues preventing the continuation of manufacturing/assembly operations, the implementation of proactive continuous improvement projects, and engaging support of appropriate enterprise functions for technically/complexity/globally challenged projects.
A Day in the Life
• The primary focus is identifying and driving a) resolution of issues that impede keeping the business running, and b) continuous improvement projects proactively by overseeing and driving attainment of best in class:
o Design of manufacturing processes, procedures and production layouts for assemblies, equipment installation, processing, machining and material handling.
o Design arrangement of machines within plant facilities to ensure most efficient and productive layout.
o Design sequence of operations and procedures for the fabrication of tools and equipment and other functions that affect product performance.
o Adaptation of machine or equipment design to factory and production conditions.
o Incorporation of inspection and test requirements into the production plan.
o Development of manufacturing processes that are applicable to statistical process control.
• Inspect performance of machinery, equipment, and tools to verify their efficiency, and investigate and initiate corrective action of problems and deficiencies to ensure product quality and delivery.
• Drive the planning, procurement, and deployment of capital assets on assigned projects as well as their associated validation planning & execution.
• Ensure processes and procedures are in compliance with regulations.
• Drive or support activities leading to reducing or eliminating manufacturing performance losses (e.g., standard cost variance).
• Contribute to the development and maintenance of a manufacturing technology roadmap.
• Support Medtronic’s Business Continuity Planning framework.
• Contribute to capacity long range planning (2-5 yrs.) and support Digital Transformation/Capacity reporting.
• Drive the engagement of appropriate enterprise functions to support technically/complexity/globally challenged projects, supplier risk, and cost reduction opportunities.
• Provide input to New Product Development projects on design for manufacturability, capital assets appropriation, capacity and business continuity planning.
Must Have: Minimum Requirements
Bachelor’s Degree required with 7+ years of experience or Advanced degree with 5+ years of experience.
Nice to Have:
• B.S. Mechanical Engineering, Electrical Engineering, Bioengineering, or related education.
• Minimum of 7 years of relevant experience at Sr. level or above.
• Experience in a medical device related industry and recognized as having expert level in driving through fruition large, moderately complex initiatives of strategic importance to the organization, involving large cross-functional teams (manufacturing/assembly processes optimization, new product introductions, product/process transfers, cost reduction, design changes implementation, components end of life, capacity improvements, etc.).
• Broad knowledge of business and management principles involved in strategic planning, resource allocation, leadership technique, production methods, and coordination of people and resources.
• Broad knowledge and extensive experience on Project Management.
• Excellent communication skills to interact with internal and external customers and vendors at various levels, including executive leadership, on significant matters.
• Knowledge of raw materials, production processes, quality control, costs, and other operational excellence techniques.
• Strong Mechanical Aptitude (aptitude for understanding and using machines and/or tools).
• Six Sigma/Lean certified preferred.
• Well versed in Design for Excellence (DFX) Principles.
• Knowledgeable in risk management methodologies such as DFMEA and PFMEA.
• Experience with Solid Works, AutoCAD, MS Office, MS Project.
Travel required 20-30% of the time. International travel may be required.
WORK-LIFE BALANCE
Your personal time is yours, and we respect that and the interests you pursue outside of work. We strive to enable your work-life balance with paid time off, on top of statutory holidays, and in some regions and roles you may be able to flex this allowance.
NETWORKS AND EMPLOYEE RESOURCE GROUPS (ERGS)
One of the many ways we foster our inclusive environment is through our Diversity Networks and Employee Resource Groups. Our Diversity Networks leaders are teams appointed by our CEO. They champion programs and policies that advance more women and ethnically diverse employees into leadership roles. In the U.S., we have an African Descent Network, Asian Descent Network and Hispanic Descent Network. The PRIDE network and the Medtronic Women’s Network are global communities. These unique networks are critical to ensuring the voice of the community is heard. They work closely with senior leaders and HR to create programs to further the advancement of diverse employees.
About MedtronicTogether, we can change healthcare worldwide. At Medtronic, we push the limits of what technology, therapies and services can do to help alleviate pain, restore health and extend life. We challenge ourselves and each other to make tomorrow better than yesterday. It is what makes this an exciting and rewarding place to be.
We want to accelerate and advance our ability to create meaningful innovations - but we will only succeed with the right people on our team. Let’s work together to address universal healthcare needs and improve patients’ lives. Help us shape the future.
Physical Job Requirements
The physical demands described within the Responsibilities section of this job description are representative of those that must be met by an employee to successfully perform the essential functions of this job. Reasonable accommodations may be made to enable individuals with disabilities to perform the essential functions. For Office Roles: While performing the duties of this job, the employee is regularly required to be independently mobile. The employee is also required to interact with a computer, and communicate with peers and co-workers. Contact your manager or local HR to understand the Work Conditions and Physical requirements that may be specific to each role. (ADA-United States of America)
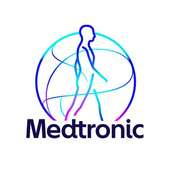
0 applies
322 views
Jobs from our Partners
Reliability System Engineer
Senior Data Engineer
Senior Machine Learning Engineer
Application Developer II, Fully Remote
Other Jobs from Medtronic
R and D Engineer - Principal
Similar Jobs
Project Lead Engineer
Lead Automation Engineer I
Lead Automation Engineer I
Lead Automation Engineer I
Quality and Reliability Engineer
There are more than 50,000 engineering jobs:
Subscribe to membership and unlock all jobs
Engineering Jobs
50,000+ jobs from 4,500+ well-funded companies
Updated Daily
New jobs are added every day as companies post them
Refined Search
Use filters like skill, location, etc to narrow results
Become a member
🥳🥳🥳 241 happy customers and counting...
Overall, over 80% of customers chose to renew their subscriptions after the initial sign-up.
Cancel anytime / Money-back guarantee