Our vision is to transform how the world uses information to enrich life for all.
Micron Technology is a world leader in innovating memory and storage solutions that accelerate the transformation of information into intelligence, inspiring the world to learn, communicate and advance faster than ever.
JR59590 OCT PH MFG ALIGNMENT SR. ENGINEER (F11)As a Central Team Alignment Engineer at Micron Technology, Inc., you will be responsible for driving improvements to manufacturing capability, delivering industry benchmark methods at the lowest cost, and managing the execution of global standards across process areas. You will execute to this by focusing on Micron’s 4 pillars, and ensure priorities are aligned to Micron business plan and/or Strategic Objective requirements across manufacturing sites.
Your objective is to leverage global internal and external resources to drive network process and equipment alignment to achieve world-class manufacturing performance. Examples include leveraging suppliers to achieve benchmark manufacturing performance, discovery and implementation of equipment and process best known methods (BKM), equipment utilization optimization, cash cost optimization, and continuous improvement project prioritization and execution globally.
You must be willing and capable of effective collaboration with SITES, Procurement, Global Quality and other OCT departments, and external suppliers to accomplish your objectives. You must also be willing and capable of international travel, as needed, to accomplish your objectives.
Tool Utilization improvement to meet BIC standards
- Execute a process to eliminate low utilization tools in Micron to hit BIC standards.
- This process must enable the cold/warm shutdown of tools, when not in need, to generate OPEX & CAPEX savings calculated through a cost model.
- Generate globally aligned warm shutdown procedures with no impact to safety & subsequent recovery to production.
- To quantify potential spare parts & manhour savings from PM count reduction.
- Tool POR-MOR gaps on major volume will need to be closed, aligned across the network & PDM updated.
Standardization of practices & BKMs in Process Areas
- Setup global area alignment teams to address chronic issues, drive improvements & eliminate wastes.
- Channel improvements and lessons learnt established from various forums, eg. TPM Forum, Excursion Review, etc. into global area forums to decide on the standards for deployment, implementation and audit.
- Design suitable matrices for each process area so that improvements impact the 4 pillars.
- Create a library of area level BKMs for Equipment & Process Engineers to search for standards involving the setup of Equipment & associated processes.
- This library must also serve the purpose to feed-forward area level BKMs to TD for process development & HVM for improvement work that will impact the 4 pillars.
PM SOP Standardization
- Align the PM Procedures across the Micron network for shared workstations.
- Integrate procedures into a system that allows Engineers & Technicians to access procedures, key recordables & measure PM Success from a tablet/notebook.
- Tie matrices to measure the effectiveness of globally aligned PM procedures.
- Put in place change management for changes to existing procedures & new PM procedures.
- Prepare the work force to move up the value chain from performing PM/CM work to achieving tool to tool matching, improving the capabilities of tools & executing tool/lot dispositions in a standardized method.
SEAL System BKM deployment & sustainment
- Implement system level BKMs in process areas globally.
- Ensure the fan out of SEAL system BKMs of high criticality and value that impact process areas through the site Task Force Teams (TFT) and local MA Engineers.
- Put in place a process to enable the speed and flexibility to transfer area level BKMs when they are ready.
- Perform one-time standardization audit as last step of TFT implementation and monitor, sustain, and control the system BKMs that impact unit process areas for the duration of one year.
Demonstrate Leadership
- Active coaching and leadership of projects. Ensure activities are well coordinated and productive.
- Provide support and guidance for BKM implementation in your area(s) of responsibility.
- Create strong morale and team spirit, shares wins and successes, foster open dialog, acknowledges team dynamics, builds on positive relationships and addresses negative ones.
- Work with the Fab groups and the Central Team to maintain alignment in your area(s) of responsibility.
Communication
- Attend area DAM meetings and update on daily plans for alignment activity to ensure coordination with daily operation priorities
- Attend weekly Area Risk Assessment Control Board Meetings to provide input on change points and assess for opportunity for worldwide sharing
- Report monthly to Area on status and progress for all alignment activity
- Regularly maintain alignment on alignment activity direction with MCT Alignment Manager and Site Area manager
- Maintain a strong and open relationship within your functional area and appropriate team members in other functional areas such as Process Integration Engineering, Quality Systems, Production Operations Management, and Purchasing.
- Promote worldwide sharing and transfer of area-specific domain knowledge.
- Communicate and respond to issues in a timely manner, with a cadence appropriate to the priority of the issue.
- Keep stakeholders and team members informed of project status, progress, and roadblocks/opportunities.
Training and Development
- Keep up to date on current Fab manufacturing processing for both R and D and manufacturing.
- Stay current with business practices at each site in your area(s) of responsibility.
- Hold self and others accountable for meeting goals and action items from projects, meetings and conversations.
- Set personal development and performance goals that are clear, measurable and in line with department and corporate goals.
- Utilize coaches/mentors to develop skills needed to take next steps in your career progression.
- Organize and utilize time and resources effectively.
- Constantly evaluate self, approach and goals.
- Demonstrate a commitment to quality in work.
- Complete assignments in an accurate, thorough and timely manner.
- Display self-motivation/initiative to complete work, training, or projects.
Safety
- Maintain knowledge of equipment and area materials safety concerns in area of focus
Qualifications and Skills include, but not limited to:
Education
- Bachelors Degree - Engineering or Related field of study
Experience
- 5 years’ experience in manufacturing plant (desirable)
- In depth knowledge of Process and Equipment perspective. Area content knowledge with experience of area methods, systems, tools. Experience across multiple areas is a plus.
- Minimum of conversational Japanese skill is preferred and the ability to lead and coordinate area teams within their site i desired
- GJS : E3 & above
About Micron Technology, Inc.
We are an industry leader in innovative memory and storage solutions transforming how the world uses information to enrich life for all. With a relentless focus on our customers, technology leadership, and manufacturing and operational excellence, Micron delivers a rich portfolio of high-performance DRAM, NAND, and NOR memory and storage products through our Micron® and Crucial® brands. Every day, the innovations that our people create fuel the data economy, enabling advances in artificial intelligence and 5G applications that unleash opportunities — from the data center to the intelligent edge and across the client and mobile user experience.
To learn more, please visit micron.com/careers
All qualified applicants will receive consideration for employment without regard to race, color, religion, sex, sexual orientation, gender identity, national origin, veteran or disability status.
To request assistance with the application process and/or for reasonable accommodations, please contact at hrsupport_tw@micron.com.
Micron Prohibits the use of child labor and complies with all applicable laws, rules, regulations, and other international and industry labor standards.
Micron does not charge candidates any recruitment fees or unlawfully collect any other payment from candidates as consideration for their employment with Micron.
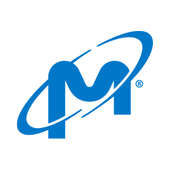
0 applies
7 views
Other Jobs from Micron Technology
SENIOR ENGINEER, OCT MODELING
Similar Jobs
CIB Lead Data Scientist
Data Engineer Team Lead
Senior QA & Automation Engineer
Senior Data Scientist
Applications Engineer
Senior Clinical AI Product Manager
There are more than 50,000 engineering jobs:
Subscribe to membership and unlock all jobs
Engineering Jobs
60,000+ jobs from 4,500+ well-funded companies
Updated Daily
New jobs are added every day as companies post them
Refined Search
Use filters like skill, location, etc to narrow results
Become a member
🥳🥳🥳 401 happy customers and counting...
Overall, over 80% of customers chose to renew their subscriptions after the initial sign-up.
To try it out
For active job seekers
For those who are passive looking
Cancel anytime
Frequently Asked Questions
- We prioritize job seekers as our customers, unlike bigger job sites, by charging a small fee to provide them with curated access to the best companies and up-to-date jobs. This focus allows us to deliver a more personalized and effective job search experience.
- We've got about 70,000 jobs from 5,000 vetted companies. No fake or sleazy jobs here!
- We aggregate jobs from 5,000+ companies' career pages, so you can be sure that you're getting the most up-to-date and relevant jobs.
- We're the only job board *for* software engineers, *by* software engineers… in case you needed a reminder! We add thousands of new jobs daily and offer powerful search filters just for you. 🛠️
- Every single hour! We add 2,000-3,000 new jobs daily, so you'll always have fresh opportunities. 🚀
- Typically, job searches take 3-6 months. EchoJobs helps you spend more time applying and less time hunting. 🎯
- Check daily! We're always updating with new jobs. Set up job alerts for even quicker access. 📅
What Fellow Engineers Say